TOP 5 Thermoforming Problems

Thermoforming is a critical process in manufacturing, where thin plastic sheets are heated to a pliable forming temperature and shaped into specific forms. Achieving high-quality results consistently requires attention to detail and understanding the common pitfalls. Here are the top 5 thermoforming mistakes and how to avoid them:
1. Drafts Cooling Down Hot Plastic Sheets
One common issue in thermoforming is drafts cooling down hot plastic sheets. This often happens when warehouse doors are opened to let forklifts pass through, or when doors and windows are opened to allow fresh air in the absence of air conditioning. Machines placed near these doors are particularly vulnerable. Additionally, air conditioning systems installed above extruders and thermoforming machines can blow directly onto the machines, affecting the plastic sheets. Even motor fans, such as those in calender roll drive motors, can blow air onto the hot sheets. To ensure consistent product quality, production halls should be equipped with entryway airlocks to prevent drafts. An effective ventilation system also adds significant value for employees by maintaining a comfortable working environment.
2. Lack of Temperature Measurement
As the name suggests, thermoforming relies heavily on precise temperature control. To produce consistent quality, it’s crucial to monitor the temperatures of the plastic sheets accurately. Temperature measurement should start at the extrusion stage and continue through the sheet entry point at the thermoforming machine to just before the thermoforming tool. By comparing and documenting these measurements, you can maintain uniform temperatures and ensure the quality of the final product.
3. Tool and Cavity Ventilation
Cleaning tools, cavities, and ejectors is an essential part of the thermoforming process. Every single vent hole must be cleaned, which can be done using various methods such as ultrasonic water baths. For stubborn dirt, small drills may be needed to clean the vent holes. Additionally, incorrect drilling of vent holes can lead to poor ventilation. Even in mold making, errors can occur. Regular and thorough cleaning of these components is vital for preventing defects and maintaining the efficiency of the thermoforming process.
4. Broken Heating Elements
Ceramic heating elements are prone to damage. Newer thermoforming machines often alert operators when the heating element resistance is out of range, indicating a potential issue. However, older machines do not have this feature. Using a thermal camera can help identify defective heating elements. Weekly checks and documentation of the heating elements are recommended to ensure they are functioning correctly and to prevent unexpected downtime.
5. Consistent Compressed Air Supply
A stable compressed air supply is essential for maintaining consistent product quality in thermoforming. The process is highly sensitive to pressure fluctuations in the system network. Any variation can lead to differences in product quality. Ensuring a constant supply of compressed air to all machines involved in the thermoforming process is crucial for achieving uniform and high-quality products.
By addressing these common mistakes, you can improve the efficiency and quality of your thermoforming process, resulting in better products and a more reliable manufacturing operation.
Share this blog article

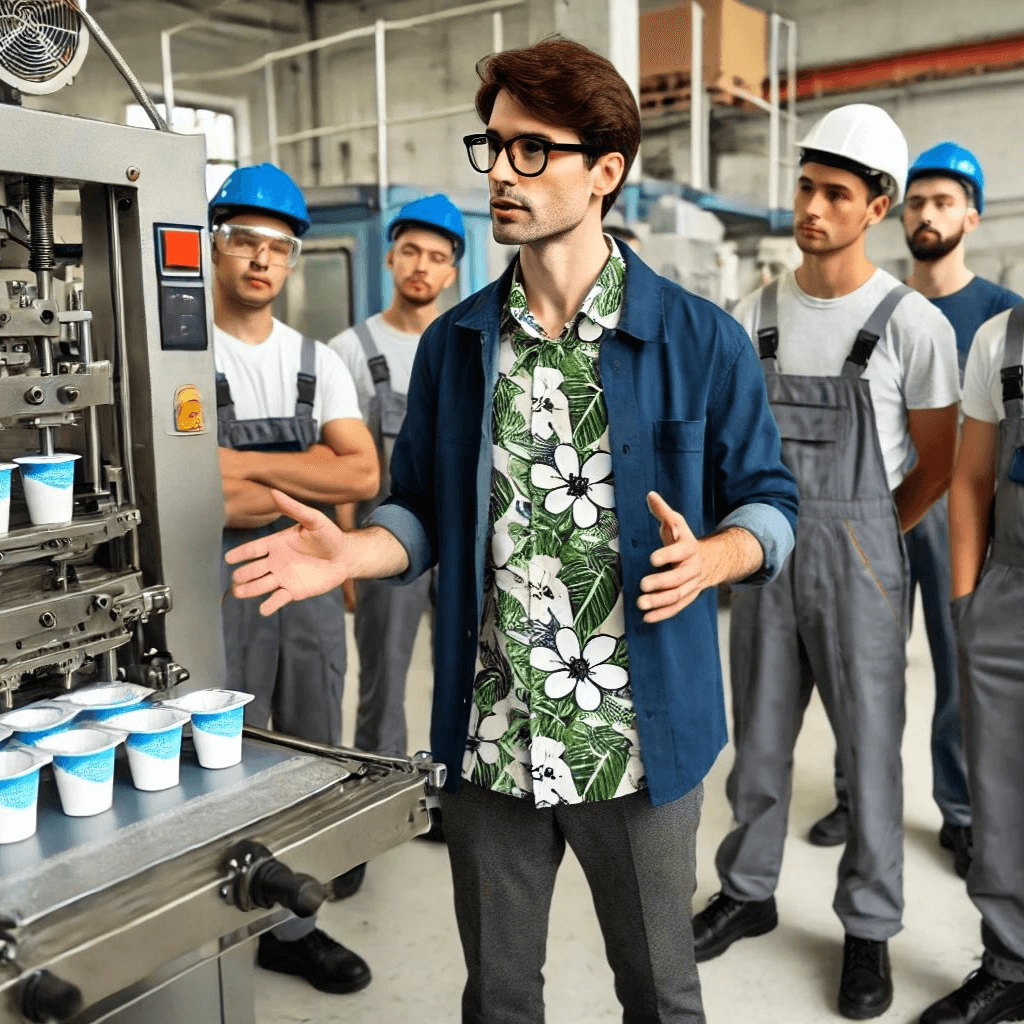
TRAINING
Unlock the Full Potential of Your Thermoforming Process with Expert Training
With our training, your staff will:
- Quickly identify and rectify errors
- Enhance operational efficiency
- Minimize downtime

OPTIMIZATION
Unlock the Full Potential of Your Thermoforming Process with Expert Training
By refining your thermoforming setup, we:
- Eliminate errors for smoother operations
- Boost overall performance
- Enhance product quality
- Minimize machine downtime
